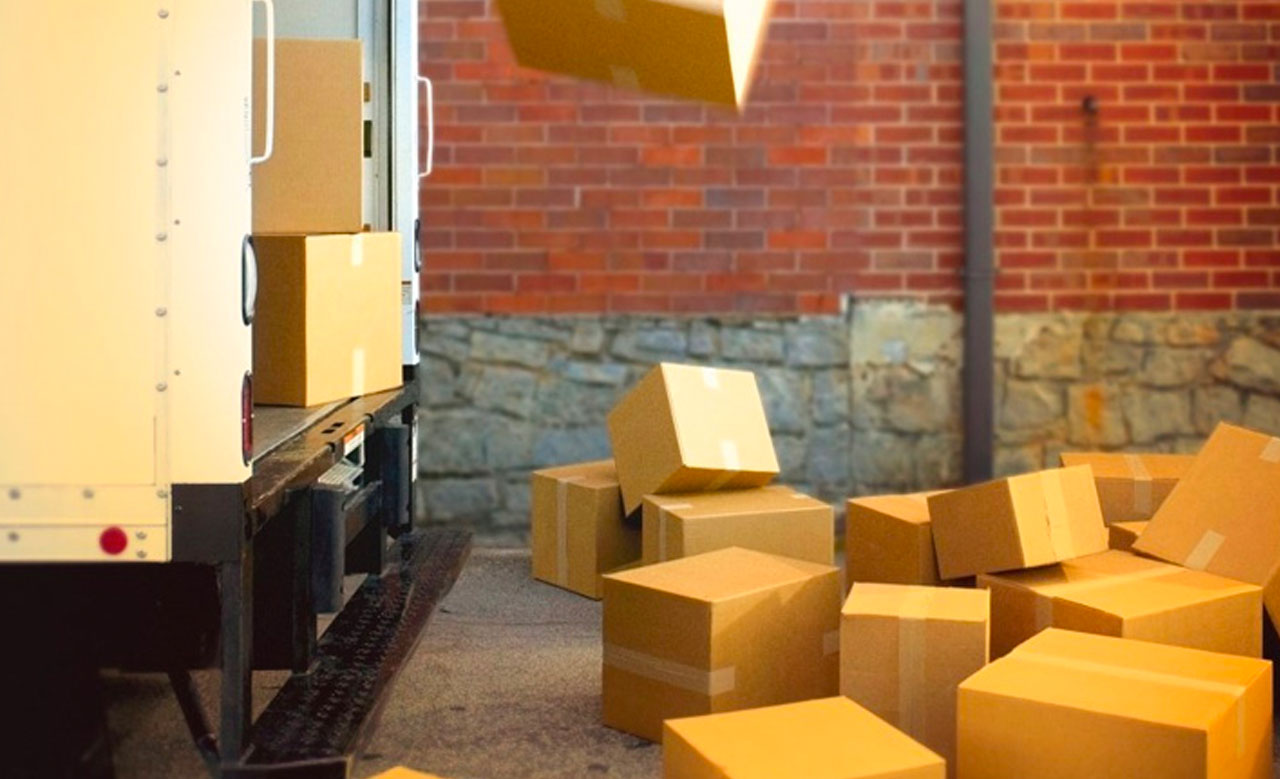
Cushioned package development test method
Optimizing your testing approach is key to understanding and ensuring product durability in real-world conditions.
Lansmont’s Six-Step Method provides a structured, proven approach to package testing, designed to help identify vulnerabilities and enhance product protection.
Follow our guide to develop a more resilient packaging solution and contact us if you need help.
วิธีการหกขั้นตอน
สำหรับการพัฒนาบรรจุภัณฑ์กันกระแทก
ผลิตภัณฑ์ + แพ็คเกจ = สิ่งแวดล้อม
บรรจุภัณฑ์ด้านประสิทธิภาพเป็นมากกว่าสิ่งที่ต้องคำนึงถึงภายหลัง แต่เป็นระบบป้องกันทางวิศวกรรมที่ออกแบบมาเพื่อให้แน่ใจว่าผลิตภัณฑ์ของคุณมาถึงโดยไม่มีความเสียหายและพร้อมใช้งาน ต้องใช้วิศวกรรมมากน้อยเพียงใดในการบรรจุผลิตภัณฑ์ของคุณ พิจารณาสูตรง่ายๆ นี้:
ขั้นตอนที่ 1 - กำหนดสภาพแวดล้อม
ขั้นตอนสำคัญในการออกแบบระบบบรรจุภัณฑ์กันกระแทกคือการกำหนดความรุนแรงของสภาพแวดล้อมที่จะจัดส่ง แนวคิดทั่วไปคือการประเมินวิธีการแจกจ่ายเพื่อระบุความเป็นอันตรายที่มีอยู่และระดับที่มีอยู่
สิ่งเหล่านี้อาจรวมถึงสิ่งต่างๆ เช่น การตกหล่นโดยไม่ตั้งใจระหว่างการจัดการ การสั่นสะเทือนของรถ แรงกระแทก อุณหภูมิที่สูงมาก ระดับความชื้น และแรงอัด
ข้อความนี้จะเน้นที่ส่วนที่มีการกระแทกและการสั่นสะเทือน แต่สิ่งสำคัญคือส่วนอื่นๆ จะต้องได้รับการพิจารณาอย่างเหมาะสมในระหว่างขั้นตอนการออกแบบบรรจุภัณฑ์ด้วย เป็นการดีที่จะติดตามทุกแพ็คเกจผ่านสภาพแวดล้อมการกระจายและสังเกตว่าเกิดอะไรขึ้นกับมัน อย่างไรก็ตาม โดยปกติแล้ว เราต้องยอมรับแนวทางอื่น สิ่งที่ดีที่สุดรองลงมาคือการใช้อุปกรณ์บันทึกบางอย่างเพื่อตรวจสอบพัสดุและ/หรือยานพาหนะระหว่างการขนส่ง หากเราทำเช่นนี้มากพอ เราจะเริ่มได้รับข้อมูลบางอย่างที่ถูกต้องทางสถิติ ซึ่งสามารถใช้อธิบายช่องทางการจัดจำหน่ายนั้นๆ ได้ เห็นได้ชัดว่ากิจกรรมจะเปลี่ยนไปในแต่ละทริป แต่โดยทั่วไปแล้วเราทราบดีว่าจะเกิดอะไรขึ้น
นี่คือแนวทางที่ดีที่สุดในการรับข้อมูลเกี่ยวกับช่องทางการจัดจำหน่ายเฉพาะ อย่างไรก็ตาม อาจเป็นวิธีที่ใช้กันอย่างแพร่หลายที่สุดคือการศึกษาข้อมูลที่เผยแพร่ที่มีอยู่ ความยากลำบากในที่นี้คือข้อมูลมักจะล้าสมัยและไม่ได้ถูกบันทึกจากสภาพแวดล้อมที่คุณจะจัดส่งพัสดุของคุณจริงๆ อย่างไรก็ตาม โดยทั่วไป อาจให้แนวทางและกฎง่ายๆ ที่จำเป็นสำหรับกระบวนการออกแบบบรรจุภัณฑ์
ไม่ควรเน้นย้ำถึงความสำคัญของข้อมูลด้านสิ่งแวดล้อมนี้มากเกินไป ในที่สุดข้อมูลนี้จะกลายเป็นส่วนหนึ่งของข้อกำหนดการออกแบบบรรจุภัณฑ์และหากไม่ได้อธิบายอย่างถูกต้อง บรรจุภัณฑ์อาจดูเหมือนล้มเหลวในการแจกจ่ายแม้ว่าจะบรรลุเป้าหมายการออกแบบแล้วก็ตาม นอกจากนี้ การบรรจุเกินอาจส่งผลให้ปัจจัยการผลิตจริงต่ำกว่าที่เลือกไว้สำหรับเป้าหมายการออกแบบ
ขั้นตอนที่ 2 – กำหนดความเปราะบางของผลิตภัณฑ์
เช่นเดียวกับน้ำหนักของผลิตภัณฑ์ที่สามารถวัดได้โดยใช้เครื่องชั่ง ความทนทานของผลิตภัณฑ์ก็สามารถวัดได้ด้วยอินพุตแบบไดนามิก เครื่องช็อตถูกใช้เพื่อสร้างเส้นโค้งขอบเขตความเสียหาย และระบบสั่นสะเทือนถูกนำมาใช้เพื่อกำหนดความถี่ธรรมชาติของผลิตภัณฑ์
ช็อก – ขอบเขตความเสียหาย
ทฤษฎีขอบเขตความเสียหายเป็นโปรโตคอลการทดสอบที่กำหนดในแง่วิศวกรรมว่าอินพุตช็อตใดจะสร้างความเสียหายให้กับผลิตภัณฑ์และสิ่งใดจะไม่สร้างความเสียหาย การกระแทกมีสองส่วนที่สามารถก่อให้เกิดความเสียหายได้ ระดับความเร่งและความเร็วที่เปลี่ยนไป การเปลี่ยนแปลงความเร็วหรือพื้นที่ภายใต้ประวัติเวลาการเร่งความเร็วของการกระแทก สามารถคิดได้ว่าเป็นพลังงานที่มีอยู่ในการกระแทก ยิ่งความเร็วเปลี่ยนแปลงมากเท่าใด ปริมาณพลังงานก็จะยิ่งสูงขึ้นเท่านั้น มีการเปลี่ยนแปลงความเร็วขั้นต่ำซึ่งต้องทำก่อนที่จะเกิดความเสียหายกับผลิตภัณฑ์
ระดับนี้เรียกว่าการเปลี่ยนแปลงความเร็ววิกฤต ต่ำกว่าการเปลี่ยนแปลงความเร็ววิกฤต ไม่มีความเสียหายเกิดขึ้นโดยไม่คำนึงถึงระดับการเร่งความเร็วอินพุต โดยพื้นฐานแล้วมีพลังงานไม่เพียงพอในบริเวณขอบเขตความเสียหายนี้ที่จะก่อให้เกิดอันตรายต่อผลิตภัณฑ์ อย่างไรก็ตาม การเปลี่ยนแปลงความเร็ววิกฤตที่สูงกว่านั้นไม่ได้หมายความว่าผลเสียหายเสมอไป หากการเปลี่ยนแปลงความเร็วเกิดขึ้นในลักษณะที่ให้ปริมาณความเร่งที่ยอมรับได้แก่ผลิตภัณฑ์ การเปลี่ยนแปลงความเร็วอาจมีขนาดใหญ่มากโดยไม่ก่อให้เกิดความเสียหาย อย่างไรก็ตาม หากความเร็ววิกฤตและความเร่งวิกฤตสูงเกินทั้งคู่ ความเสียหายจะเกิดขึ้น
ขั้นตอนที่ 3 – ความคิดเห็นเกี่ยวกับการปรับปรุงผลิตภัณฑ์
นี่คือเวลาที่จะเริ่มนึกถึงผลิตภัณฑ์และบรรจุภัณฑ์ในฐานะระบบผลิตภัณฑ์/บรรจุภัณฑ์
จากผลการทดสอบความเปราะบาง อาจเป็นที่ต้องการในการเสริมความแข็งแกร่งหรือความทนทานของผลิตภัณฑ์ แทนที่จะจัดส่งแต่ละชิ้นภายในบรรจุภัณฑ์ราคาแพง ควรระบุและจัดลำดับการแลกเปลี่ยนระหว่างต้นทุนผลิตภัณฑ์ ความน่าเชื่อถือของผลิตภัณฑ์ และต้นทุนบรรจุภัณฑ์เพื่อประสิทธิผล บ่อยครั้งที่เป็นไปได้ที่จะยกระดับความเปราะบางของผลิตภัณฑ์ด้วยการดัดแปลงเล็กน้อยหรือการเปลี่ยนแปลงการออกแบบ ซึ่งอาจเพิ่มต้นทุนเล็กน้อยให้กับแต่ละผลิตภัณฑ์ แต่หากความต้องการด้านบรรจุภัณฑ์ลดลงอย่างมาก ราคารวมของระบบจะลดลง
ความสามารถในการปรับใช้การปรับเปลี่ยนผลิตภัณฑ์อาจแตกต่างกันไปขึ้นอยู่กับบรรยากาศภายในบริษัทแต่ละแห่ง และตำแหน่งของบุคคลที่พยายามทำให้สำเร็จ สำหรับบางบริษัท ข้อเสนอแนะประเภทนี้ต่อนักออกแบบผลิตภัณฑ์เป็นขั้นตอนอย่างเป็นทางการที่ใช้ในการพัฒนาผลิตภัณฑ์ใหม่ทั้งหมด ซึ่งช่วยให้ผลิตภัณฑ์มีความน่าเชื่อถือมากขึ้น มีคุณภาพดีขึ้น และยังช่วยลดต้นทุนบรรจุภัณฑ์ให้ต่ำที่สุด
ในสถานการณ์อื่นๆ โดยเฉพาะอย่างยิ่งเมื่อบรรจุภัณฑ์ได้รับการพัฒนาโดยซัพพลายเออร์ภายนอก แทบจะเป็นไปไม่ได้เลยที่จะโน้มน้าวให้บริษัทเห็นว่าการเปลี่ยนแปลงผลิตภัณฑ์เป็นไปเพื่อผลประโยชน์สูงสุดของพวกเขาเอง อย่างไรก็ตาม การนำเสนอแนวคิดเหล่านี้และรับบทบาทนักการศึกษาตามความจำเป็นยังคงมีความสำคัญ หากเป็นไปได้ ให้พยายามระบุการแลกเปลี่ยนระหว่างการเปลี่ยนแปลงผลิตภัณฑ์เล็กน้อย ค่าความน่าเชื่อถือและค่าซ่อม และค่าบรรจุภัณฑ์
ขั้นตอนที่ 4 – การประเมินประสิทธิภาพของวัสดุกันกระแทก
โดยทั่วไป ข้อมูลประสิทธิภาพของวัสดุควรมีให้จากผู้ผลิตวัสดุ อย่างไรก็ตาม ในบางกรณี อาจจำเป็นต้องสร้างข้อมูลประเภทนี้ ซึ่งเกี่ยวข้องกับการตรวจสอบทั้งลักษณะการดูดซับแรงกระแทกและการส่งผ่านแรงสั่นสะเทือนของวัสดุ
ควรสังเกตว่าข้อมูลที่สร้างขึ้นโดยวิธีการเหล่านี้ใช้ได้กับวัสดุกันกระแทกเท่านั้น และอาจไม่จำเป็นต้องเหมือนกับการตอบสนองที่ได้รับในแพ็คที่สมบูรณ์ นอกจากนี้ พื้นที่ชิ้นงานทดสอบ ความหนา อัตราการบรรทุก และปัจจัยอื่นๆ จะส่งผลต่อประสิทธิภาพที่แท้จริงของวัสดุในทุกสถานการณ์ สิ่งนี้หมายความว่าสามารถใช้ข้อมูลเพื่อให้การคาดเดาทางวิทยาศาสตร์ที่ดีที่สุดสำหรับการออกแบบบรรจุภัณฑ์เริ่มต้น แต่อาจยังต้องมีการปรับแต่งบางอย่างอยู่
ประสิทธิภาพการลดแรงกระแทก
เส้นโค้งกันกระแทกอธิบายวัสดุในแง่ของการชะลอตัวที่ส่งไปยังวัตถุที่ตกลงบนวัสดุนั้นที่โหลดคงที่ต่างกัน เส้นโค้งกันกระแทกหนึ่งเส้นถูกสร้างขึ้นสำหรับวัสดุแต่ละประเภท ความหนาของวัสดุ และความสูงของการตก
โดยพื้นฐานแล้วขั้นตอนการทดสอบคือการทิ้งแท่นวางน้ำหนักที่ระบุจากความสูงของหยดที่ทราบลงบนเบาะที่มีพื้นที่และความหนาของตลับลูกปืนที่กำหนดไว้ล่วงหน้า การชะลอตัวของแท่นวางที่กระทบจะถูกตรวจสอบและบันทึกโดยมาตรวัดความเร่ง หยดห้าหยดจากความสูงหยดหนึ่งๆ กระทำกับตัวอย่างที่การโหลดความเค้นคงที่ที่กำหนด
ค่าเฉลี่ยของค่าการชะลอตัวที่อ่านได้จากสี่หยดล่าสุดคือค่าที่ใช้ในการวางแผนจุดโค้งของเบาะแต่ละจุด การเพิ่มน้ำหนักบนแท่นวางจะทำให้ความเค้นคงที่บนวัสดุกันกระแทกสามารถเปลี่ยนแปลงได้ ผ่านชุดการทดสอบที่การโหลดแบบสถิตต่างๆ ข้อมูลจะถูกสร้างขึ้นและนำเสนอในรูปแบบของเส้นโค้งกันกระแทก (ดูรูปที่ 10) มีการทดสอบการโหลดแบบคงที่อย่างน้อยห้าครั้งเพื่อพล็อตแต่ละเส้นโค้ง โดยใช้ตัวอย่างใหม่ในการโหลดแต่ละครั้ง
ขั้นตอนที่ 5 – การพัฒนาแพ็คเกจกันกระแทก
ขณะนี้ผู้ออกแบบบรรจุภัณฑ์มีข้อมูลทั้งหมดที่จำเป็นในการปกป้องผลิตภัณฑ์ในระหว่างการจัดจำหน่ายอย่างเพียงพอ ขั้นตอนที่ 1 กำหนดประเภทของอินพุตที่พัสดุจะได้รับระหว่างการจัดส่ง
ขั้นตอนที่ 2 กำหนดความทนทานของผลิตภัณฑ์และความสามารถในการทนทานต่อปัจจัยแวดล้อม ขั้นตอนที่ 3 ประเมินความทนทานเพื่อให้สามารถออกแบบผลิตภัณฑ์ใหม่ได้ ขั้นตอนที่ 4 กำหนดลักษณะการทำงานของวัสดุบรรจุภัณฑ์ ถึงเวลาแล้วที่จะรวมข้อมูลนี้เข้ากับการออกแบบบรรจุภัณฑ์
ช็อต – การออกแบบบรรจุภัณฑ์
ขั้นแรก รวบรวมส่วนโค้งของเบาะรองนั่งสำหรับวัสดุเบาะรองนั่งที่เลือก สิ่งสำคัญคือต้องตรวจสอบว่าความสูงหล่นที่ส่วนโค้งของเบาะถูกสร้างขึ้นเหมือนกับความสูงของส่วนโค้งการออกแบบที่เลือกในขั้นตอนที่ 1 จากนั้น ค้นหาระดับการเร่งความเร็ววิกฤตที่กำหนดในขั้นตอนที่ 2 บนเส้นโค้งของเบาะแต่ละส่วน ลากเส้นแนวนอนผ่านจุดนี้ ส่วนใดๆ ของเส้นโค้งที่อยู่ต่ำกว่าเส้นความเร่งวิกฤตจะระบุช่วงโหลดคงที่ซึ่งวัสดุควรส่งผ่านน้อยกว่าความเร่งวิกฤต ดูรูปที่ 12
การสั่นสะเทือน – การออกแบบบรรจุภัณฑ์
สำหรับการพิจารณาการสั่นสะเทือน เราจำเป็นต้องรวบรวมเส้นโค้งการขยาย/ลดทอนสำหรับวัสดุที่เลือก ค้นหาความถี่ธรรมชาติของผลิตภัณฑ์ที่ต่ำที่สุดในแต่ละเส้นโค้ง และวาดเส้นแนวนอนทั่วโครงร่าง ส่วนใดๆ ของเส้นที่ขยายเข้าไปในโซนลดทอนจะระบุช่วงการโหลดแบบคงที่ซึ่งวัสดุควรลดการสั่นสะเทือนที่ความถี่ที่ผลิตภัณฑ์มีความไวมากที่สุด ดูรูปที่ 13
เมื่อระบุการโหลดแบบคงที่ซึ่งดูเหมือนจะให้การป้องกันแรงกระแทกและการสั่นสะเทือนที่เพียงพอแล้ว ก็สามารถเลือกวัสดุและความหนาได้ การโหลดแบบคงที่จริงซึ่งถูกเลือกสำหรับบรรจุภัณฑ์นั้นขึ้นอยู่กับหลายปัจจัย อย่างไรก็ตาม การออกแบบที่การโหลดแบบคงที่สูงสุดที่เป็นไปได้หมายถึงการใช้วัสดุน้อยลง เมื่อข้อควรพิจารณาอื่นๆ เช่น การคืบอัดมีความสำคัญ การออกแบบให้โหลดคงที่ต่ำที่สุดเท่าที่จะเป็นไปได้อาจรับประกันได้ รูปที่ 14 แสดงวิธีการคำนวณปริมาณวัสดุที่ต้องใช้รอบๆ ผลิตภัณฑ์เพื่อให้ได้โหลดคงที่ที่ต้องการ
ขั้นตอนที่ 6 – ทดสอบระบบผลิตภัณฑ์/บรรจุภัณฑ์
เมื่อการออกแบบบรรจุภัณฑ์เสร็จสิ้น ระบบบรรจุภัณฑ์ต้นแบบจะได้รับการทดสอบเพื่อให้แน่ใจว่าเป็นไปตามเป้าหมายการออกแบบทั้งหมด
ช็อก – การทดสอบบรรจุภัณฑ์
บรรจุภัณฑ์ต้องสามารถตกลงมาจากความสูงของการออกแบบที่กำหนดไว้ในขั้นตอนที่ 1 และส่งน้อยกว่าความเร่งวิกฤตไปยังหน่วย มาตรวัดความเร่งที่ติดตั้งกับส่วนที่แข็งของผลิตภัณฑ์ใกล้กับจุดศูนย์ถ่วงสามารถใช้เพื่อตรวจสอบระดับความเร่งที่ส่งผ่านวัสดุกันกระแทกไปยังผลิตภัณฑ์ได้ มีการเลือกตำแหน่งที่เข้มงวดเพื่อให้สามารถสังเกตข้อมูลป้อนเข้าของผลิตภัณฑ์โดยรวมระหว่างการกระแทก และเปรียบเทียบโดยตรงกับผลลัพธ์ของการทดสอบ Step Acceleration อาจเป็นที่ต้องการในการตรวจสอบตำแหน่งเพิ่มเติมในระหว่างการทดสอบ เช่น ส่วนประกอบที่สำคัญบางอย่าง อย่างไรก็ตาม วิธีเดียวที่มีประสิทธิผลในการประเมินประสิทธิภาพของแพ็คเกจคือการตรวจสอบตำแหน่งที่เข้มงวด ตัวบรรจุภัณฑ์เองไม่ได้เปลี่ยนการตอบสนองของผลิตภัณฑ์ต่ออินพุตที่กำหนดโดยตรง แต่สามารถปรับเปลี่ยนอินพุตซึ่งสุดท้ายจะไปถึงผลิตภัณฑ์ได้
การหยดแบบแบนมักจะคิดว่าเป็นการหยดที่รุนแรงที่สุดเท่าที่จะเป็นไปได้ในแง่ของระดับความเร่งที่ส่งไปยังผลิตภัณฑ์ Flat drops เน้นอินพุตทั้งหมดตามแกนเดียวของยูนิต และพลังงานเพียงเล็กน้อยจะสูญเสียไปกับการกดทับมุมหรือขอบของบรรจุภัณฑ์ หรือกับการหมุนบรรจุภัณฑ์ ดังนั้นจึงใช้ Flat drops เพื่อวัดประสิทธิภาพของระบบบรรจุภัณฑ์
อย่างไรก็ตาม การตกหล่นที่มุมและขอบมักจะสร้างความเสียหายให้กับโครงสร้างของบรรจุภัณฑ์ ซึ่งการหยดแบบแบนๆ ที่คล้ายกันจะไม่เกิดขึ้น หยดประเภทนี้มักจะใช้เป็นส่วนหนึ่งของลำดับการทดสอบเพื่อตรวจสอบความสามารถในการยึดของบรรจุภัณฑ์ในระหว่างการขนส่ง
Field-to-Lab® Consulting
Lansmont's experienced consulting services team deliver field measurement studies, data analysis, and test specification development.